کاهش آب تمیز مصرفی خط تولید کاغذ بستهبندی با سیکل بسته
مجموعه کاغذ کار کسری، مجموعه کاغذسازی با 100% کاغذ بازیافتی (OCC¬ ) است که در حال حاضر قابلیت تولید روزانه 305 تن با سه خط تولید را دارد و در آینده نزدیک با راه اندازی خط تولید 4، توانایی افزایش ظرفیت تولید تا 500 تن روزانه را خواهد داشت.این مجموعه با راه اندازی یک سیستم تصفیه¬خانه بیولوژیکی در سال 1388 با ظرفیت تولید روزانه وقت 100 تن موفق شده بود پرتن آب مصرفی را از استاندارد جهانی 10 مترمکعب به 7 مترمکعب کاهش دهد و در حال حاضر با ظرفیت تولید روزانه 305 تن و با افزودن سیستم¬های به روزتری همچون EDR¬ و MBR¬ این مقدار را به 4 مترمکعب پرتن کاهش داده است و در صدد است تا با راه اندازی کامل طرح جدید تصفیه آب و پساب به مقدار 2 مترمکعب پرتن برسد. هرچند افزایش بازچرخانی آب مشکلات عدیده¬ای را به همراه دارد ولی با وجود تکنولوژی های به روز دنیا امکان نزدیک شدن به سیکل ZLD شدنی است و مجموعه های بزرگ کاغذسازی دنیا همچون کاغذسازی های آلمان طی 40 سال گذشته توانسته اند پرتن مصرفی آب را از متوسط 50 مترمکعب پرتن به 5 مترمکعب پرتن کاهش دهند. لذا مجموعه کسری تنها کاغذسازی در صنعت داخلی کشور خواهد بود که توانسته است سیستم بازچرخانی آب فرآیند خود را به سیستم بسته یا ZLD نزدیک کند.
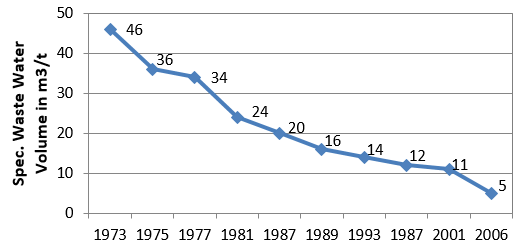
همانطور که مشاهده می شود این مقدار از 50 مترمکعب پرتن تولیدی به نزدیک 5 مترمکعب پرتن کاهش یافته است. این کاهش چشمگیر به دلیل فشارهای اقتصادی بوده که بر اساس قانون GETL از تقریبا 40 سال پیش اعمال شده است.کارخانه¬های کاغذ موظف بودند تا مبلغ شخصی بر اساس واحد آلودگی خروجی تصفیه شده کارخانه بپردازند که این واحد مبنی بر پارامترهایی همچون TSS، COD ، مواد سمی و مضر برای ماهی و فلزات سنگین (Cd – Cu – Cr – Hg – Ni) می¬باشد .
نمودار 2 میزان پساب تولیدی کاغذسازی¬های مختلف در آلمان را در سال¬های اخیر نشان می¬دهد. همانطور که ملاحظه می شود مدرن ترین کارخانه ها در رنج 22 – 5 مترمکعب پرتن قرار دارند.شایان ذکر است در کارخانه های قدیمی مقدار این مشخصه به دلیل طراحی های غیر استاندارد و تکنولوژی پایین تر می تواند خیلی بیشتر باشد.
نمودار 2. میزان پساب تولید صنایع مختلف کاغذ در آلمان
نمودار 3 حالت¬های مختلف تخلیه پساب خروجی بر اساس تناژهای کاغذسازی¬های آلمان( با جمع حدود 20 میلیون تن سالانه) نشان می¬دهد. تا قبل از سال 1963 خروجی خط تولید تنها با روش های مکانیکی (ته نشینی یا فیلتراسیون) تصفیه می شده و در نهایت به صورت مستقیم به بیرون از کارخانه انتقال می یافته است ولی امروزه 4 رویه مختلف جهت تخلیه و دفع پساب خروجی وجود دارد :
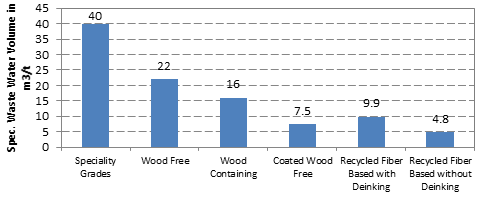
- تخلیه مستقیم پساپ تصفیه شده مکانیکی و بایولوژیکی ( 75 % تولید کاغذ)
- تخلیه مستقیم پساب تصفیه شده مکانیکی بدون تصفیه بیولوژیکال (3% مربوط به کارخانه های بسیار کوچک)
- تخلیه غیرمستقیم پیش تصفیه شده مکانیکی که در نهایت در یک تصفیه جمعی(multi-user) بصورت بایولوژیکال تصفیه شده و به محیط زیست منتقل می شود (18%)
- رویه بدون دفع پساب یا ZLD که یک چرخه کاملا بسته از آب فرآیند است و از رویه های به روزی است که مورد توجه قرار گرفته است . در این چرخه آب فرآیند بصورت سیستم داخلی کارخانه تصفیه شده و مجددا مورد استفاده قرار می گیرد (4%) نمودار 3. حالتهای مختلف دفع پساب به صورت درصدی براساس صنایع کاغذسازی آلمان
2. اساس چرخه بسته یا ZLD :
فشارهای اقتصادی، زیست محیطی و سازمانهای NGO، منجر شده تا سیستمهای آب کارخانه نزدیک به یک سیستم بسته شود.فرآیند بسته شدن چرخه آب در کارخانههای کاغذ قهوهای در آلمان و کارخانههای تولید تست لاینر در فرانسه و کارخانه های Corrugating از کاغذ بازیافتی شروع شده است و در حال حاضر در کارخانههای تولید کاغذ روزنامه، Printing/Writing وCoated در حال اشاعه است.
زمانیکه صحبت از طراحی سیکل کاملا بسته می شود بایستی از ریسکهای احتمالی آن آگاهی کامل داشت. از ریسکهای ابتدایی میتوان خوردگی، انتشار ترکیبات بوزا، افزایش تشکیل لجن، کاهشretention ، افزایش مواد افزودنی، تشکیل رسوب، مشکلات runability، کاهش کیفیت تولید و افزایش پیچیدگی فرآیند تولید کاغذ و غیره نام برد.
بعضی از پارامترها و ریسکها به راحتی قابل کنترل بوده و برخی مشکلات بیشتری دارد همچون رسوب کلسیم کربنات که می تواند منجر به بلاک شدن نازل های شاور ، رسوب در لوله ها و بروی لوزام پوششی ماشین کاغذ( همچون وایر، فلت) گردد.همچنین یکی از عوامل اصلی خوردگی کلراید و سولفور میباشد. به این منظور جهت کاهش ریسک خوردگی در مصارف پایین آب تمیز بایستی از مصرف مواد شیمیایی شامل کلراید و سولفات خودداری شود.یکی دیگر از ریسک های خوردگی ناشی از فعالیت بی هوازی بیولوژیکی در کارخانه می باشد که علاوه بر آن منجر به تشکیل بوی نامطبوع در محیط و کاغذ تولیدی خواهد شد(تحت شرایط بی هوازی سولفات به هیدروژن سولفید- H2S تبدیل میشود).
از طرف دیگر سیستم بسته چرخش آب مزایایی در پی دارد یکی از مزیتهای اصلی آن کاهش آب تمیز مصرفی تا حداقل مطلق 5/1 مترمکعب پرتن تولیدی است که منجر به کاهش هزینههای جاری کارخانه، از بابت کاهش فرار الیاف کاغذ و مواد شیمیایی، دمای بالاتر چرخه آب فرایند تولید خواهد شد(شایان ذکر است کاهش مصرف آب تمیز، دمای آب سفید فرآیند کاغذ را افزایش میدهد که منجر به بهبود آبگیری آب از کاغذ بخش فورمینگ کاغذ یا وایر و افزایش غلظت خمیر کاغذ بعد از قسمت پرس می شود و در نهایت منجر به کاهش میزانانرژی مصرفی در بخش خشککنها میگردد) و لذا از تخلیه و دفع پساب خروجی جلوگیری شده و متعاقبا هزینههای تصفیه پساب کاهش خواهد یافت.یکی دیگر از مزایای با اهمیت سیستم بازچرخانی بسته کاهش هزینههای پساب خروجی در کشورهایی مثل آلمان است(همانطور که اشاره شد در کشورهایی همچون آلمان به ازای هر واحد پساب خروجی هزینه ای دریافت می شود ).
بطور کلی کارخانههای کاغذسازی با محدودیتهایی جهت تامین آب تمیز و مصرف آن(کیفیت و حجم)، تخلیه پساب خروجی و هزینههای تامین آب و تصفیه پساب روبرو هستند؛لذا مجموعههای تولید کاغذ با وجود چنین محدودیتهایی میتوانند با اجرای سیکل بازچرخانی آب فرآیند مزایای بیشتری بدست آورند .
شکل 1 شماتیک ساده ای از یک کارخانه کاغذ با چرخه کاملا بسته را نشان میدهد که در آن مجموعه آماده سازی خمیر و ماشین کاغذ بعنوان تجهیزات مرکزی میباشد.چرخه آب فرآیند براساس سیکل کوتاه و سیکل بلند از آب زلال شده فرآیند از سمت وایر و پرس می باشد که برای رقیق سازی در واحد خمیرسازی و آب شاور در برخی از قسمت های ماشین کاغذ استفاده می شود.آب تمیز بر اساس حجم آب تبخیر شده از قسمت خشک کن و آب اتلافی از پسماندیست که قابل استفاده در بخش خمیرسازی نمیباشد.
شکل 1. سیکل شماتیکی چرخه بسته تولید کاغذ
همچون سیکل بستهای بدون تصفیه با مشکلات شدیدی به دلیل غلظت بالای مواد حل شده آلی و غیرآلی (همچون تبدیل کربوهیدرات ها به COD و بوی نامطبوع ونمکها(هدایت الکتریکی EC) ) روبرو خواهد شد.یکی از تکنولوژیهایی که توانسته بر این مشکلات غلبه کند تکنولوژی معروف به کلیه یاKidney است که در برخی از شرکتهای آلمانی پیاده شده است.شکل 2 این سیکل را با تکنولوژی Kidney بصورت شماتیکی نشان میدهد .
شکل 2. سیکل تولید کاغذ با سیستم کلیوی یا Kidneys
این تکنولوژی یک تصفیه موثر و پیشرفته آب فرآیند را تضمین میکند که در نهایت در وهله اول منجر به حذف مواد آلی حل شده(کاهش COD) و در وهله دوم منجر به کاهش مواد غیر آلی حل شده(کاهش نمک ها یا EC) می شود. به دلیل کارایی این تکنولوژی اکثر مشکلات (قریب به همه مشکلات) سیستم بسته در دراز مدت می تواند کنترل شود(مثل کاهش خوردگی، انتشار بوی نامطبوع، مشکلات Runability و جلوگیری از افت کیفیت تولید).
تکنولوژیهای مختلفی از Kidney از برندها و مارکتهای مختلف در دنیا وجود دارد اما تکنولوژی متداول شامل فرآیندهای بیولوژیکی (هوازی یا بی هوازی یا ترکیبی از هردو) میباشد.خارج از آلمان تکنولوژی ممبران یکی از فرآیندهای مورد توجه است ولی این فرآیندها نیاز به زلالسازی آب چرخه تولید تا کاهش بسیار زیاد مواد جامد معلق،جهت جلوگیری از بلاک شدن ممبرانها دارد. در این مورد سیستم فلاکسازی و رسوبسازی آب به همراه مواد افزودنی آلی و/یا غیرآلی ضروری میباشد.همچنین زمانیکه انرژی ارزان در دسترس باشد، سیستم تبخیر نیز امکان پذیر می باشد ،البته یک فرآیند مناسب برای رسیدن به آب چرخشی نسبتا تمیز، ازنزنی و بایوفیلتر می باشد .
صنعت کاغذسازی آلمان یکی از اولین ها در پیادهسازی سیکلهای بسته از سال 1973 میلادی بوده است.در ابتدا این کارخانهها مجهز به تکنولوژی Kidney نبوده و زلالسازی ساده برای جداسازی فیبرهای کاغذ از آب گردشی و استفاده مجدد مواد جامد معلق بعنوان فیلر و فیبر مصرفی در تولید صورت میگرفته است. در بازه زمانی کوتاه ،آب در حال چرخش این مجموعه ها مشکلاتی همچون انتشار بو و خوردگی تجهیزات در پی داشته است.بنابراین تقریبا نصفی از این کارخانهها چرخه آب خود را تا مصرف آب تمیز 5 مترمکعب پرتن مصرفی باز کردند و بعضی از این کارخانهها بدلیل ادامه دادن سیکل بسته مجبور به استفاده از مقدار زیادی بایوساید جهت کنترل تشکیل شدید لجنها(ناشی از تجزیه کربوهیدراتها) شدند.
در سال 1995 اولین کارخانه سیکل کاملا بسته در آلمان به همراه راکتورهای بیولوژیکی بعنوان تکنولوژی Kidney در تصفیه آب چرخشی فرآیند تولید معادل یک سوم کل حجم آب گردشی تولید شروع بکار نمود.امروزه تقریبا 8 کارخانه بزرگ تولید کاغذ بسته بندی چنین سیستم بستهای در آلمان مشغول بکار هستند که دوتا از این مجموعهها مجهز به تکنولوژی Kidneys می باشند که بصورت مختصر به آنها اشاره می شود :
2-1- مجموعه کاغذسازی Zulpich mill of kappa paper
یکی از این کارخانهها، کارخانه Zulpich آلمان با تولید سالانه 410.000 تن تست لاینر از کاغذ بازیافتی میباشد. در بازه 1975 تا 1995 این مجموعه با سیستم بدون دیسشارژ و بدون تکنولوژی kidney فعالیت داشت ولی در نهایت به دلیل مشکلات خوردگی و بوی نامطبوع، در اوایل دهه 1990 مدیریت این مجموعه، تصمیم به مجهز کردن سیستم تصفیه جهت کاهش مواد آلی حل شده (COD) نمود. شکل 3 شماتیک سیستم Kidney را در این کارخانه نمایش داده شده است .
شکل 3. سیستم تصفیه پساب خط تولید در کارخانه Zulpich آلمان
به دلیل COD بسیار بالا در این نوع سیکل گردشی (بیشتر از ppm 30.000) شرایط برای تصفیه بیهوازی ایده آل است لذا در این طرح از یک راکتور UASB، یک سیستم زلال سازی اولیه جهت جداسازی مواد جامد معلق و یک زلالسازی ثانویه جهت جداسازی لجن خروجی سیستم های هوازی دیده شده است و در نهایت جهت کاهش TSS خروجی تصفیه خانه تا ppm20، از سیستم فیلترشنی استفاده شده است. جدول شماره 1 تاثیر استفاده از این تکنولوژی را در این کارخانه نشان میدهد.
Parameter |
Unit |
Before Start-Up of "kidney" |
After Start-Up of "kidney" |
PH |
6.3 |
7.2 |
|
Electical Conductivity |
mS/cm |
9.0 |
5.0 |
COD |
mg/l |
32,800 |
6,400 |
Water Hardness |
dH |
375 |
70 |
Calcium |
mg/l |
2,650 |
505 |
Sulphate |
mg/l |
1,350 |
375 |
Chloride |
mg/l |
430 |
485 |
Acetic Acid |
mg/l |
6,300 |
890 |
Propionic Acid |
mg/l |
600 |
355 |
n-Butyric Acid |
mg/l |
350 |
<20 |
جدول 1. تاثیر سیستم Kidney بر کیفیت آب گردشی خط تولید کاغذ Zulpich آلمان
جالبترین پارامتر هدایت الکتریکی است که از 9 به 5 ms/cm کاهش یافته چرا که تکنولوژی Kidney تاثیری بر حذف نمک ندارد. البته بخشی از نمکهای سختی در سیستم تصفیه بیولوژیکی رسوب کرده و غلظت نمک را در حد قابل قبولی نسبت به غلظت سولفات و کلسیم نگه داشته است در حالیکه غلظت کلراید تغییر چندانی نکرده است. علاوه بر این مواد آلی (اسیدهای چرب) به صورت چشمگیری کاهش یافته است که در نهایت کاهش چشمگیر COD تا 80% در پی داشته است.
2-2- مجموعه کاغذسازی Dusseldorf Mill of Julius Schulte Sohne
یکی دیگر از کارخانههای به روز یافته در زمینه سیکل بدون دیسشارژ، کارخانه خصوصی(Julius schulte) با تناژ متوسط سالانه 90.000 تن از کاغذ بازیافتی میباشد. این کارخانه قبل از بستن سیکل گردشی خود، دارای سیکلی با میزان 2/3 مترمکعب پرتن پساب و معادل مصرف آب تمیز نزدیک به 5 مترمکعب پرتن بوده است که بصورت یک کارخانه با تخلیه غیرمستقیم پساب و در ارتباط با سیستم تصفیه مرکزی Dusseldorf فعالیت داشته است و بعد از پیاده سازی طرح جدید با تکنولوژی kidney بصورت سیکل کاملا بسته فعالیت میکند. در شکل 4 شماتیکی از این کارخانه بعد از پیادهسازی این طرح آورده شده است .
شکل 4. سیستم kidney پیاده شده در کارخانه Julius schulte
آب فرآیند در این کارخانه ابتدا توسط یک شناورسازی میکرونی نظیر سیستم Krofta، زلال شده (در شکل نشان داده نشده است) و سپس جهت تزریق مواد و کنترل دما به واحد کولینگ و pre-acidification ارسال می شود و بعد از این مرحله به یک برج راکتور UASB از نوع سیرکوله داخلی یا راکتور انتقال مییابد و بعد از این مرحله به واحد هوازی با دو راکتور هوادهی با هوای فشرده منتقل میشود و با افزایش PH ناشی از خروج گاز CO2، کلسیم کربنات رسوب میکند که یکی از مزیتهای این سیستم نسبت به سیستم لجن فعال میباشد. آخرین مرحله این طرح شامل سیستم فیلترشنی است جهت اطمینان از TSS خروجی مجموعه در کمتر از ppm 10 است. جدول 2 دادههای مربوط به مراحل مختلف این طرح را نشان میدهد.
Influent Process Water Treatment Plant |
|||
Hydraulic Load |
m3/d |
600 - 1,200 |
|
COD Load |
kg/d |
2,000 - 6,500 |
|
Calcium Load |
kg/d |
300 - 650 |
|
IC- Reactor |
|
|
|
COD Loading Rate |
kg/m3d |
15 - 40 |
|
COD Reduction Rate |
% |
40 - 60 |
|
Biogas Production |
m3/d |
200 - 1,400 |
|
Areation Reactors |
|
|
|
COD Reduction Rate |
% |
10 - 30 |
|
Calcium Elimination Rate |
% |
50 - 90 |
جدول 2. کیفیت آب گردشی در سیستم Kidney خط تولید کاغذ Julius schulte
همانطوریکه مشاهده میشود میزان بار آلودگی ورودی بسته به کیفیت کاغذ بازیافتی مورد استفاده و میزان تزریق مواد افزودنی در پروسه تولید و نوع/عملکرد ماشین کاغذ متغیر است و کاهش COD در راکتور IC ، 60-40% و راکتور هوادهی 30-10% و میزان حذف کلسیم 90-50% می باشد و در مجموع کاهش کلی COD 85-70% است. جدول 3 پارامترهای مهم قبل و بعد از این سیستم نشان می دهد .
Parameter |
Unit |
Before Start-Up of "kidney" |
After Start-Up of "kidney" |
PH |
|
6.6 |
6.6 |
Electical Conductivity |
mS/cm |
2.7 |
5.1 |
COD |
mg/l |
5,070 |
4,150 |
Water Hardness |
dH |
62 |
66 |
Calcium |
mg/l |
420 |
450 |
Sulphate |
mg/l |
360 |
475 |
Chloride |
mg/l |
215 |
920 |
Acetic Acid |
mg/l |
760 |
480 |
Propionic Acid |
mg/l |
330 |
305 |
Butyric Acid |
mg/l |
<20 |
<20 |
AOX |
mg/l |
0.34 |
0.54 |
جدول 3. کیفیت آب گردشی در سیستم
همانطورکه ملاحظه میشود مقدار هدایت الکتریکی آب بعد از پیاده سازی این طرح تقریبا دو برابر شده است و غلظت یون کلراید افزایش چشمگیری داشته است چرا که سیستمی جهت حذف این آنیون(همچون تکنولوژی ممبران) وجود ندارد. دیگر پارامترها همچون COD، کلسیم و سولفات تقریبا ثابت مانده، علی رغم اینکه استیک اسید کاهش قابل ملاحظه ای داشته است.
همچنین نتایج مثبت این سیکل بسته در آنالیزهای کاغذ قابل مشاهده بوده است بطوریکه خواص استحکامی کاغذ با پیاده سازی این سیستم تغییر نکرده و شکایتی از جانب مشتریان بابت تغییر در کیفیت کاغذ دریافت نشده است و بطور کلی این سیستم تاثیری در کیفیت کاغذ و انتشار بوی نامطبوع نداشته و در فرآیند تولید نیازی به استفاده از بایوساید جهت حفظ Runability و عملکرد تولید نبوده است و مصرف مواد افزودنی در همان سطح ثابت (قبل از سیستم بسته چرخش آب) باقی مانده است .
3. سیستم پیاده شده Kidney در مجموعه کاغذکار کسری جهت کاهش مصرف آب:
در سیستم فعلی تصفیه آب و پساب مجموعه کسری شامل دو فاز قدیم و جدید می باشد .فاز قدیم با سرمایه گذاری 4 میلیارد تومانی در سال 1388 بر اساس تصفیه 3000 مترمکعب روزانه شامل سیستم پیش تصفیه میکروفلوتیشن(سیستم کرافتا)، pre-Acidification، راکتور IC، حوضچه هوادهی و زلال ساز نهایی بوده که قابلیت بازچرخانی 60% پساب تصفیه شده را به خطوط تولید داشته است که با توجه به تولید وقت دو خط تولید با ظرفیتتولید سالانه 27.000 تن از کاغذ 100% بازیافتی OCC) منجر به کاهش حجم آب تمیز مصرفی از 12-10مترمکعب پرتن به 8-7 مترمکعب پرتن گردید .شماتیکی از این طرح در شکل 5 آورده شده است.
شکل 5. سیستم kidney پیاده شده در کارخانه کاغذکسری در سال 1388
فاز جدید براساس طرح توسعه خط 3(با یک تکنولوژی به روز و دقیق) و با توجه به شرایط اقلیمی(کم آبی استان یزد و کیفیت پایین آب موجود) ارزیابی و با کمک یک شرکت مشاورهای خارجی طراحی گردید و در سال 96-1395 با سرمایه گذاری 3.500.000 یورویی تجهیزات خریداری و شروع به نصب گردید که در حال حاضر علی رغم مشکلات تحریم تا حدود 80-70% تجهیزات بهره برداری گردیده است و هم اکنون با ظرفیت تولید 100.000 تن سالانه از کاغذ 100% OCC، پرتن آب مصرفی به 5-4 مترمکعب کاهش یافته و در نهایت با راه اندازی کامل این سیستم، امید است این عدد به 3-2 مترمکعب پرتن برسد .(شماتیکی از طرح جدید در شکل آورده شده است). همچنین این مجموعه در صدد است با راه اندازی خط 4 با تناژ کلی سالانه 150.000 تن میزان مصرف آب تمیز را تا حد 2 مترمکعب پرتن حفظ کند.
فاز جدید بر اساس تصفیه آب و پساب شامل سیستمهای EDR، پیش تصفیه مکانیکی و شیمیایی(با کمک سیستم میکروفلوتیشن کرافتا)،Pre–Acidification ، راکتور IC، سختی گیری به روش فرار گاز CO2، هوادهی و MBR میباشد. همچنین شایان ذکر است در این طرح ریجکتها و پسماندهای خطوط تولید حتی المقدور آبگیری شده و آب زلال شده به سیکل تولید باز می گردد. همانطور که ملاحظه میشود، طرح جدید این مجموعه تقریبا تکمیل شده طرح اجرایی کارخانه Dusseldorf آلمان است به نحوی که در مجموعه کسری از دو سیستم بسیار قوی ممبرانی جهت حذف کلراید و حذف باکتریهای باقیمانده در پساب خروجی تصفیه شده استفاده شده است(شکل 6).
شکل 6. طرح جدید سیکل بسته تولید در کارخانه کاغذ کسری
جداول 4 و 5 به ترتیب کیفیت آب و پساب این مجموعه را قبل و بعد از EDR و MBR نشان می دهد. همانطوریکه مشاهده میشود، با وجود سیستم EDR، مشکل تغلیظ یون کلراید که در سیستم Kidney شرکت کاغذسازی Dusseldorf آلمان وجود داشت، در این مجموعه کنترل شده است و میزان باکتریهای باقیمانده در خروجی سیستم MBR به طور قابل ملاحظهای کاهش مییابد.
جدول 4. کیفیت آب قبل و بعد از سیستم EDR
|
Feed |
Product |
ion |
[mg/l] |
[mg/l] |
Na+ |
1063 |
101 |
K+ |
4.7 |
0.4 |
Ca2+ |
350 |
17 |
Mg2+ |
66 |
6 |
Ba2+ |
0 |
0 |
F- |
0 |
0 |
CL- |
1298 |
123 |
HCO3- |
732 |
70 |
NO3- |
15 |
1.5 |
SO4 2- |
575 |
55 |
T-hardness(mgCaCO3/lit) |
<1300 |
<100 |
Conductivity(µS/cm) |
<5000 |
<700 |
TDS |
<4500 |
<400 |
جدول 5. کیفیت آب قبل و بعد از سیستم EDR
Parameter |
Unit |
Before MBR Start-Up |
After MBR Start-Up |
PH |
|
7.5 |
8-8.5 |
Electical Conductivity |
mS/cm |
9000 |
<5000 |
COD |
mg/l |
200-300 |
<100 |
Total Hardness |
mgCaCO3/lit |
2500 |
<300 |
Ca2+ |
mg/l |
800 |
<150 |
Total Coliform bacteria |
MPN/100ml |
1100< |
<40 |
TSS(after ETP) |
mg/l |
<100 |
<1 |
TSS(after Paper machine) |
mg/l |
6,000 |
<2500 |
در نمودار 4 نیز مصرف آب تمیز(بر حسب پر تن تولیدی) در سالهای اخیر آورده شده است که نشانگر کاهش چشمگیر این شاخص از متوسط 12 به 4 مترمکعب پر تن کاغذ تولیدی طی 10 سال اخیر است.
نمودار 4.مصرف آب تمیز بر حسب تن تولیدی مجموعه کاغذ کسری در سالهای مختلف
4. نتیجه گیری:
در دهههای اخیر به دلیل فشارهای اقتصادی و زیست محیطی، صنایع بزرگ کاغذ بستهبندی دنیا به سمت طراحی و پیادهسازی سیستمهای بسته و بدون دیسشارژ پساب تمایل پیدا کردهاند. تجربه کشورهای بزرگ در این صنعت بخصوص کشور آلمان نشان میدهد با استفاده از سیستمهایی همچون سیستم Kidney این امر امکانپذیر است. مجموعه کاغذکار کسری نیز با توجه به واقع شدن در شرایط جغرافیایی خاص، مسئله کم آبی در کشور و تعهدات زیست محیطی و براساس طرحهای توسعه خطوط تولید خود دست به اقدام بزرگ در زمینه طراحی و پیادهسازی سیستم بسته چرخش آب(یا بدون دیسشارژ) زده است. به طوریکه موفق شده است طی 10 سال گذشته مصرف آب تمیز خطوط تولید خود را از متوسط 12 به 4 مترمکعب پر تن تولیدی کاهش دهد. طرح مجموعه کسری تقریبا تکمیل شده طرح اجرایی کارخانه Dusseldorf آلمان است و با کمک سیستمهای ممبرانی EDR و MBR، مشکلات طرح آن کارخانه آلمانی نظیر تغلیظ یون کلراید و باکتریهای باقیمانده قابل کنترل است. شایان ذکر است علیرغم کاهش مصرف آب تمیز، این مجموعه توانسته کیفیت کاغذ تولیدی خود را حفظ نموده و بر مشکلاتی همچون تشکیل شدید لجن در ماشین کاغذ، بو نامطبوع کاغذ و رسوبگذاری و غیره غلبه کند و در زمینه پیادهسازی یک سیستم بسته با بازچرخانی کامل پساب تصفیه شده، تنها کارخانه تولید کاغذ بستهبندی در صنعت ایران باشد.
5. مراجع:
- Diedrich, K., Hamm, U. and Knelissen, J.H. (1997). Biological water treatment cycle in a paper mill with closed water cycle. Das Papier 51(6A), 163-169.
- Bulow, C., Pingen, G. and Hamm, U. (2003). Closing of the water circulation of a paper mill with regarding to the calcium problematic. Ipw-Das Papier(1), 31-39
- Hamm, U., Schabel, S. (2007). Effluent-free papermaking: industrial experiences and latest developments in the German paper industry. Water Sci Technol. 55(6), 205-11.